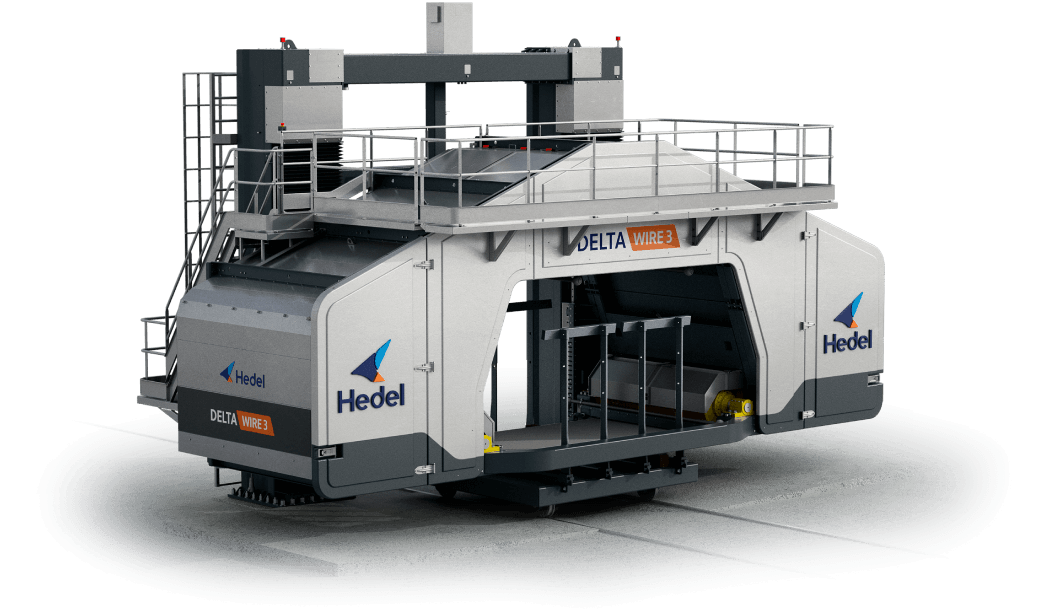
Delta Wire is built on a robust and steady structure. Assembled on two columns this manufacturing concept reduces maintenance cost and assists on the assembly and disassembly of the wire gears.
The cutting head has a triangular geometry which allow that the wires twist less in the circuit, work close to each other supported by conducting wheels generating less vibration and way more precision.
With the Delta Wire System developed by Hedel a meaningful increase in durability of the diamond coated wires, cutting speed and quality of cut sheets was conquered.
The triangular geometry defines the concept of economic multiwires
Up and down motion
The two columns are made of stainless steel plates on a welded structure in a box shape. The sliding guides are coated by special high quality steel rectified and interchangeable which slide on adjustable cursors.
The movement is obtained through the trapezoid washer-spindle and spindle-washer. In machines with over 44 wires the up and down loads are assisted by 2 hydraulic cylinders.
Every trapezoid washer-spindle and spindle-washer systemare lubricated by an oil re-circulation system and protected of environment contamination by a double nest.
We developed a fast lifting system for machine models over 44 wires, with a special servicer motor to lift the machine structure in under or up to 5 minutes increasing the productivity and reducing the idle time between the changes from one load to the next.
Traction set, moved set, guides and axles
The traction set is composed by a drum with a diameter of 1.260 mm activated by a motor responsible to start the movement of translation of the diamond coated wires. The drum is made in carbon steel and in it the traction set profiles are attached. The profiles are independent parts and can be easily replaced in case of wear and tear.
This set can be provided in two configurations:
Bearing system: Utilizing a special bearing technologically developed for this application.
Self-sliding bushing: Maximum resistance to compression, operational temperature up to 200 o C. It operates dry or submersed. It absorbs chocks and misalignment. Excellent resistance to wearing, abrasion and corrosion in a hostile environment with the presence of water mixed with rock dust, it becomes an extremely effective solution.
The cutting guides wheels are made in the diameter of 780 mm in carbon steel and are responsible for the quality and precision of the rock sheets cutting. They are the drum closer to the block consequently the ones that are most affected by attrition among diamond coated wires, polyurethane profile and rock residue. The profile of these drums can be replaced individually in a fast and easy manner. It is an ideal system to reduce the time the machine remains idle.
The axles are made from carbon steel and are heat treated up to a temperature of 980 o C going through a sudden controlled temperature drop to stabilize the material after this process : machining, finishing and zinc coating.
Tensioning
The secret of a fast and precise cut is in the correct tensioning of the wire. The Delta Wire system delivers what the market asks for and need: productivity and quality.
Hedel’s solution is an individual tensioning system utilizing special forged rolling wheels over robust rocker forks activated by sensitive and precise pneumatic cylinders. The great advantage of the pneumatic system is the sensitiveness of a low load that each diamond coted wire needs never surpassing the tensioning max limit.
A pneumatic central the several stages of operation and cylinder pressure. Every wire needs the same tensioning load individually. This way the adjustment is done by a single sensor.
Delta Wire has the best tensioning system which allows meticulous recoil of the wires when they are not operating correctly or when in contact with harder parts of the rock. It doesn’t force the wire and balances its tensioning weight until its stabilized again avoiding breakage of the wire. This factor is only possible with the pneumatic system which when the normal work load surpasses the normal load it compresses and recoil the wire until the end.
Another advantage is that the pneumatic cylinder are made from aluminum and do not oxidize as hydraulic pistons which are made of steel and due to an aggressive environment do generating tensioning errors and damage to metal sheets contaminated by oil leakage.
Rubber parts interchangeability
One of the features of a winning machine is certainly the easiness of maintenance and one of the main advantages of Delta Wire is the easy exchange of the polyurethane profiles on the pulleys.
The solution is through a series of polyurethane bands over the ones which the grooves to let the diamond have coated wires run. Every spool has an exterior cover with a series of slots in which will be attached elastically the inferior polyurethane profiles. Whit this solution, once the grooves are wore it becomes very simple the replacement of the bands, since its enough to remove the used ones and replace them without the need to dismantle the machine drums.
Water spots
Delta Wirer is equipped with lubrication, cooling and cutting area cleaning system that guarantees the best operation conditions of the diamond coated wires within every slot and the complete removal of residues. The system consists in 9 wire washing points which the advantages are: Less machine incrustation, reduction of wearing on the polyurethane cover of the wheels, longer service life and higher efficiency of the diamond coated wire.
Cowling (armor) and protection
The cowling and covers are made of stainless steel providing a longer service life to the equipment, reducing the corrosion effects and tearing of the multiwire system. The frontal part has closing cover increasing the operational safety which also protects the machine and the working environment, reduces the dust cloud and water generated by the cutting operation. The protections and footbridge were developed to provide comfort and safety to the operator. To change the cutting wires Delta Wire is equipped with inspection points positioned in a strategic way allowing a fast and easy replacement of wires and avoiding that they get exposed on the outer side which would give the chance of an eminent accident.